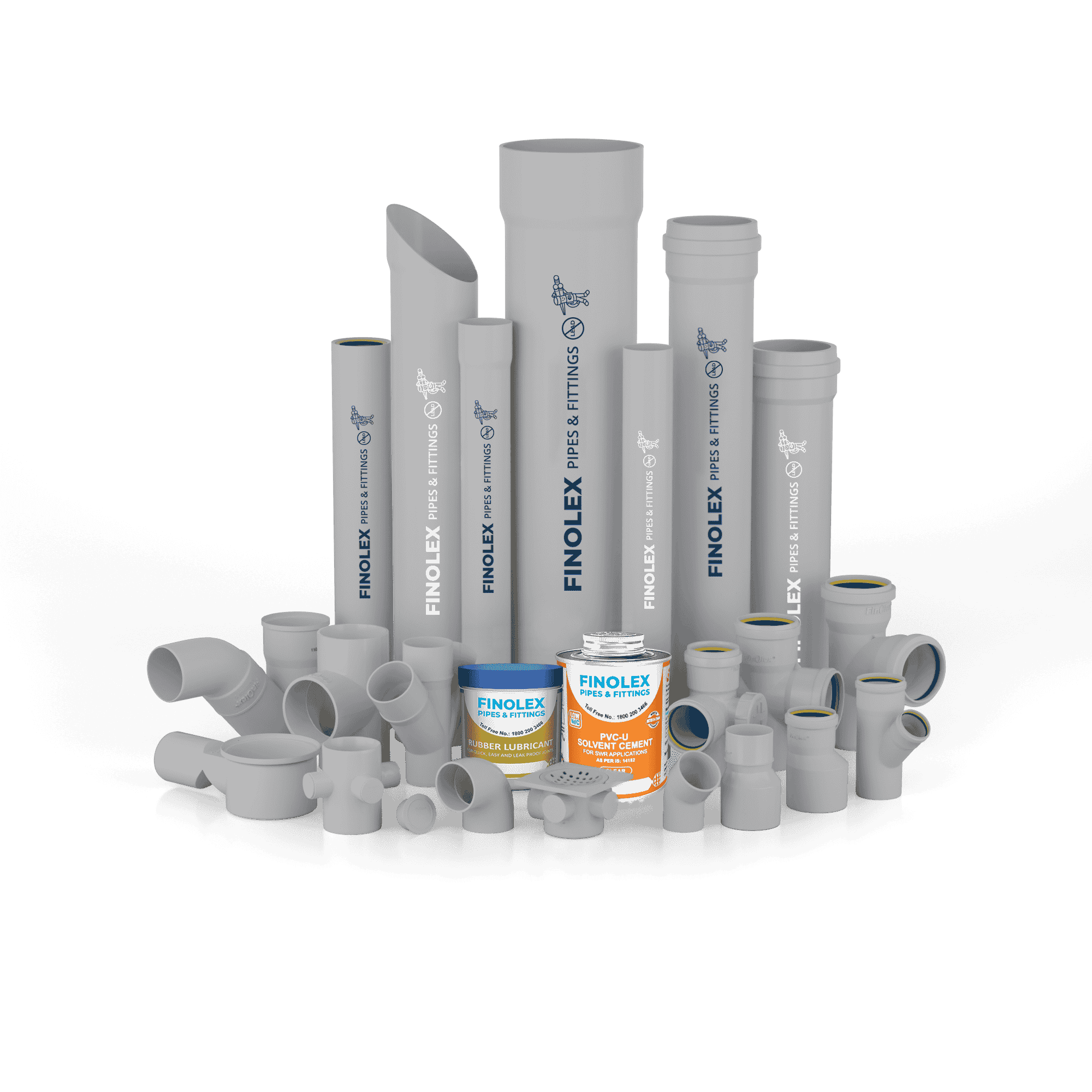
SWR Pipes & Fittings
Finolex SWR pipes and fittings are specially designed and manufactured using high grade raw material and are an ideal solution for efficient removal of waste in the drainage system.
SWR pipes and fittings are used for non-pressure plumbing applications, such as transportation of soil, waste and rainwater, non-pressure industrial drainage applications, and waste discharge systems in residential and commercial complexes, resorts, and hospitals.
Finolex PVC SWR pipes system is an ideal replacement for CI and GI piping systems because it is lightweight, economical, non-corrosive and UV stabilised, which makes it highly durable. It offers extreme climate resistance and a smooth inner surface to prevent clogging.
Our stringent quality assurance approach across all stages of manufacturing gives the product a high-degree of reliability making Finolex PVC SWR pipes a preferred choice of leading MEP consultants, architects, builders, plumbing contractors, plumbers, and quality-conscious people across the country.
SWR pipes are available in various sizes ranging from 40 mm to 160 mm. These pipes are manufactured as per IS 13592 and are offered with Integrated Ringfit and Selfit socket systems.
SWR pipes are offered in two primary types; type A for rainwater and vents, and type B for soil and waste discharge. Fittings are available in various sizes from 40 mm to 160 mm in Selfit and integrated ring type sockets. Fittings are manufactured as per IS 14735.
SWR SELFIT PIPES
Conforming to IS 13592
Finolex Selfit SWR pipes are manufactured in a way that one end of the pipe is plain, while the other
is self-socketed and facilitates ease in jointing by the use of Finolex Solvent Cement.
SWR SELFIT FITTINGS
Conforming to IS 14735
Fittings are available in various sizes from 40 mm to 160 mm in selfit sockets.
SWR PIPES WITH INTEGRATED RINGS
Conforming to IS 13592
Finolex SWR pipes and fittings support easy installation as the Integrated Ring pre-fitted in the groove of the socket remains permanently positioned. The joint is made simply by pushing the spigot end into the socket end, without the use of any Solvent Cement. Finolex lubricant should be used for easy insertion. The ring forms a leak proof joint and absorbs the linear expansion and contraction, keeping the seal intact.
SWR FITTINGS WITH INTEGRATED RINGS
Conforming to IS 14735
SWR pipe and Fittings are available in various sizes from 75 mm to 160 mm in integrated ring type sockets.
SELFIT FITTINGS
INTEGRATED RINGS FITTINGS
Application





Technical Details
JOINTING
• For Selfit Pipes & Fittings:
![]() |
1. Measuring : Measure the required length of pipe and marking done. |
![]() |
2. Cutting : The pipe must be cut in a square shape. The base of the fitting socket needs a rubber ring to seal it, since an angled cut may result in leakage. |
![]() |
3. Deburring & Chamfering : All the burr must be removed from the inside and outside of the pipe with a knife, file or de-burring tool. A 10° – 15° chamfer must be made at the end of the pipe. |
![]() |
4. Cleaning : The surface dirt, grease or moisture must be removed with a clean dry cloth. |
![]() |
5. Check Dry Fit : Using light pressure, the pipe should be inserted one third to half the way into the socket. Note that pipes and fittings that are too tight or too loose should not be used. |
|
6. Solvent Cement Application : An even layer of cement should be applied to the outer side of the pipe and a medium layer of the plumbing solvent cement to the inside of a fitting. |
![]() |
7. Assembly : Join the pipe and fitting socket till in contact with the socket bottom. Hold the pipe and fitting together until the pipe does not retract. The excess cement can be removed from the exterior surface of the pipe and fitting. A properly made joint will show a continuous bead of cement around the perimeter of the pipe and fitting. |
• For Pipes & Fittings with Integrated Rings:
![]() |
1. Measuring : Measure the required length of pipe and marking done. |
![]() |
2. Cutting : The pipe must be cut in a square shape. The base of the fitting socket needs a rubber ring to seal it, since an angled cut may result in leakage. |
![]() |
3. Deburring & Chamfering : All the burr must be removed from the inside and outside of the pipe with a knife, file or de-burring tool. A 10° – 15° chamfer must be made at the end of the pipe. |
![]() |
4. Cleaning : The surface dirt, grease or moisture must be removed with a clean dry cloth. |
![]() |
5. Check Dry Fit : Using light pressure, the pipe should be inserted one third to half the way into the socket. Note that pipes and fittings that are too tight or too loose should not be used. |
|
6. Solvent Cement Application : Apply lubricant even layer on rubber ring prior to insertion. |
![]() |
7. Assembly : Push the pipe in integrated ring socket end. |
FINOLEX SOLVENT CEMENT & LUBRICANT
1. SOLVENT CEMENT
PVC-U Solvent Cement for SWR applications and meets
ml | 100 | 250 | 500 | 1000 |
Container | Tin | Tin | Tin | Tin |
2. RUBBER LUBRICANT
Finolex Rubber Lubricant is used for installation of (Manufactured as per IS 14182 SWR pipes and fittings with integrated rings.
ASTM D 2564 standard)
gms | 50 | 100 | 250 | 500 | 1000 |
Container | Plastic Container |
Outside diameter of pipe (mm) |
Outside diameter of pipe (inches) |
Approx No. of Joints/Ltr. of Finolex Solvent Cement |
|||
40 | 11/4” | 175 | |||
50 | 11/2” | 130 | |||
63 | 2” | 125 | |||
75 | 21/2” | 100 | |||
90 | 3” | 75 | |||
110 | 4” | 50 | |||
140 | 5” | 35 | |||
160 | 6" | 28 |
Additional information
THERMAL EXPANSION
SWR pipes and fittings are not concealed and are always exposed to external surfaces and sunlight. The diurnal
temperature varies at many places between 5°C to 20°C, which naturally leads to expansion & contraction of
pipes. This thermal expansion is required to be taken into consideration in the design of a sanitation system.
The expansion & contraction occurs more in vertical lines. Therefore SWR pipes with integrated rings are most
suitable for a vertical stack. It is necessary to maintain an expansion gap at rubber ring joints to allow movement
of pipe due to thermal expansion.
Please measure the socket length by a measuring tape and mark along the pipe. During installation, push the
pipe firmly into the socket fitted with an integrated ring till the gap between the mark on the spigot and
socket is about 10mm, to allow for thermal expansion. Finolex recommends selfit jointing for all horizontal
wastewater lines. Selfit fittings makes the system cost effective, without affecting the performance. Horizontal
pipes require closer support compared to vertical pipes. Pipe brackets/pipe clips must be used to anchor
expansion joints.
PIPE CLIP SUPPORT SPACING DISTANCE
Pipe Size (mm) | 75 | 90 | 110 | 160 |
Spacing For Horizontal Pipe Size (mtrs) | 1.0 | 1.0 | 1.0 | 1.2 |
Spacing For Vertical Pipe Size (mtrs) | 1.8 | 1.8 | 1.8 | 1.8 |
CERTIFICATIONS & APPROVALS
• Pipes are manufactured conforming to IS 13592 (Bureau of India Standards).
• Fittings are manufactured as per IS 14735 (Bureau of India Standards).
• Tested & approved by Central Institute of Plastics Engineering & Technology (CIPET).
FAQs
-
What is the meaning of SWR pipe?
SWR stands for Soil, Waste and Rainwater Pipe for building drainage systems.
-
What are the applications of the SWR system?
SWR system comes in three applications 1. for Building (Soil & waste) drainage discharge 2. For rainwater discharge 3. For venting foul gases and odor.
-
What is the SWR drainage system?
It is a complete assembly of SWR pipes, fittings which is joined with solvent cement or rubber ring.
-
Why is the Finolex SWR pipe the best?
Finolex SWR pipes are the best because they are manufactured by using Finolex’s own PVC resin. Finolex SWR pipes are UV stabilized and are manufactured using state of the art technology and automation.
-
IS code for PVC SWR System?
SWR Selfit/IRR (integrated rubber ring) pipes conform to IS:13592. Fittings are manufactured as per IS 14735.
-
Types of SWR Pipes?
SWR comes in 2 types- 1. Selfit pipes with solvent cement jointing 2. Integrated rubber rings (IRR) with jointing done by using lubricant for easy insertion. The EPDM ring provides watertight joints. .
-
Do SWR Pipes come with different wall thicknesses?
Yes. SWR comes in 2 types in both the variants (Selfit & IRR)- - Type A - For use in ventilation pipework and rainwater applications. - SWR Type B - For use in soil waste and rainwater discharge systems. (Higher wall thickness than Type A).
-
Are SWR Pipes safe, when exposed to sunlight?
Finolex SWR Pipes are UV stabilised during the manufacturing process itself, making them safe and durable when exposed to sunlight.
-
Can Agri pipes (IS4985) be used in place of SWR pipes?
Agri Pipes are recommended for underground pressurized applications and hence are not UV stabilized. SWR Pipes are generally exposed to sunlight and are UV stabilized for a longer life.
-
Normally where SWR IRR pipes should be used and why?
For high rise/ multi-story buildings where the piping system is exposed to sunlight, technically only SWR IRR pipes should be used, as the integrated ring ensures leak-proof joints that can sustain thermal contraction and expansion and it is easy for maintenance and repair works whenever required.
-
Can SWR Pipes, which are exposed to sunlight be painted, if yes, which paint?
Only water-based paint should be used in such cases.
-
Do you have SWR pipes & fittings in Push-fit type?
Our SWR IRR Pipes are with pre-fitted rings for faster installations and are of the push-fit type and thus are user and plumber friendly, especially while the plumber is working at a height.
-
Where are SWR type B pipes recommended for use?
SWR type B has a higher wall thickness (than type A), so it is recommended in soil and wastewater discharge systems.
-
Is your SWR system safe in incidents like fire?
Finolex SWR pipes and fittings do not support fire and provide good resistance to combustion.
-
Is SWR safe, where normally bathrooms & WCs are cleaned with acids?
Finolex SWR is non-reactive to acids, alkalis, effluents, salt and minerals, thus it can be safely used.
-
Where can the SWR system be used?
In waste discharge systems in residences, commercial complexes, resorts, hospitals, academic institutes. This is an ideal replacement for CI & GI piping. - It can also be used for venting gases and odors in domestic plumbing. Rainwater transportation and rainwater harvesting for residential and commercial buildings. Non-pressure industrial drainage applications based on chemical compatibility.
-
I am constructing an independent bungalow with G+1. Can I use SWR Selfit pipes?
Yes, given your requirement, you may use SWR Selfit pipes.
-
Can I use solvent cement for jointing SWR IRR pipes?
No. Rubber Lubricant should be used to facilitate easy insertion and the pre-fitted EPDM ring offers watertight and leaks proof joints.